工业设备生命周期的智能化革命:预测维护AI软件的核心价值
在全球制造业迈向智能化与可持续化的进程中,工业设备的维护模式正经历一场深刻的变革。传统的被动式维修与定期维护逐渐被基于人工智能的预测性维护(Predictive Maintenance, PdM)取代,这一技术通过实时监测、数据分析与机器学习,不仅能够提前发现设备潜在故障,还能优化维护策略,显著延长设备生命周期。据研究,工业设备的非计划停机成本可占企业年收入的15%-20%,而预测维护AI软件通过将故障率降低30%-50%,可将设备使用寿命延长20%以上。这一技术的核心在于数据驱动的决策能力,结合物联网、边缘计算与深度学习,为工业设备管理提供了从“事后应对”到“主动预防”的全面升级。
一、技术基础:数据与算法的双重驱动
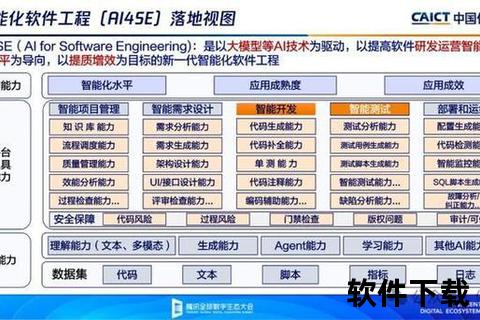
**数据采集与处理:工业设备的“生命体征”监测**
预测维护AI软件的核心基础是设备运行数据的全面采集。通过部署振动、温度、压力、电流等多维度传感器,系统实时获取设备状态信息,形成涵盖全生命周期的健康数据集。例如,半导体制造设备通过每15分钟的振动信号监测,可精准捕捉轴承磨损或电机失衡的早期征兆。数据的价值不仅在于数量,更在于质量。数据预处理技术(如缺失值填充、噪声过滤和特征降维)至关重要。以风力涡轮机为例,其振动信号需经过Hilbert包络解调和全矢融合处理,才能有效提取反映轴承寿命的关键特征。
**算法模型:从传统机器学习到深度学习**
预测维护的算法体系经历了从支持向量机(SVM)、随机森林到深度学习的迭代。早期研究中,随机森林因其对高维数据的处理能力被广泛用于电机定子绕组短路故障预测,准确率可达89%。而深度学习模型(如LSTM和CNN)在时间序列数据分析中表现更为突出。例如,锂电池剩余寿命预测中,结合CNN的振动特征提取与LSTM的时序建模,预测误差可控制在3%以内。值得注意的是,工业场景中“小样本数据”的挑战推动了迁移学习与联邦学习的应用。某钢铁企业通过跨场景通用特征库构建,实现了干熄焦起重机故障识别准确率达95.3%。
二、应用场景:从寿命预测到维护闭环
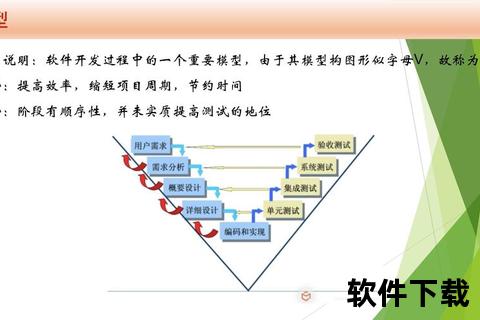
**设备寿命预测:从物理模型到数据驱动**
传统寿命预测依赖物理模型,需要专家经验与复杂公式推导,而AI技术通过数据拟合与模式识别实现了突破。例如,航空发动机的剩余使用寿命(RUL)预测中,基于机理框架与数据驱动的混合模型(如“极限学习机+贝叶斯推理”)可将预测精度提升至92.6%。在锂电行业,通过融合设备层级性能仿真与BIM数字孪生技术,某企业制冷站系统的能效比(COP)从3.9提升至5.5,设备寿命延长29%。
**故障诊断与维护策略优化**
AI不仅预测故障,还能提供决策支持。在机床主轴故障案例中,AI平台通过实时分析加工数据,提前7天预警断刀风险,减少非计划停机70%。维护策略的动态调整是延长设备寿命的关键。例如,高负荷设备采用高频次预防性维护,而稳定设备则延长维护周期,这种差异化策略使某汽车零部件制造商年均维护成本降低289万元。
三、挑战与优化:技术落地的现实瓶颈
**数据质量与系统兼容性难题**
工业数据的异构性(如PLC协议差异、传感器采样率不统一)导致数据融合困难。某风电企业因环境恶劣导致振动传感器数据丢失率高达15%,最终通过自适应硬件设计与多协议兼容方案解决。模型泛化能力不足仍是痛点。研究表明,同一算法在不同设备间的预测误差波动可达20%以上,需通过行业特征库构建与持续学习优化。
**模型可解释性与实时性平衡**
深度学习模型的“黑箱”特性限制了其在安全敏感场景的应用。例如,核电设备维护要求故障原因可追溯,而随机森林的特征重要性分析(如Gini指数)更易被接受。边缘计算的引入提升了实时性。凌华科技的Phoenix GM3S系统通过边缘端振动信号处理,将数据分析延迟从分钟级压缩至秒级,满足半导体厂房实时监控需求。
四、未来方向:边缘智能与跨行业协同
**边缘计算与5G的深度融合**
未来预测维护系统将向“云-边-端”协同架构演进。例如,某锂电企业通过边缘节点执行振动特征提取,仅将关键数据上传至云端训练模型,带宽消耗降低80%。5G网络的高可靠低时延特性(uRLLC)进一步支持实时控制,如数控机床的刀具磨损补偿指令可在10ms内下达。
**跨行业知识迁移与标准化**
工业设备的多样性要求算法具备跨场景适应能力。硕橙科技通过构建覆盖200+工业场景的声振特征库,使同一模型在泵机与压缩机中的故障识别准确率差异小于5%。ISO 13374标准的推广为数据接口与模型评估提供了统一框架,加速了预测维护技术的规模化落地。
迈向零故障的工业未来
预测维护AI软件的价值不仅体现在设备寿命的延长,更在于其对制造业价值链的重构。从半导体设备的振动监测到风电齿轮箱的声纹分析,这一技术正在将“故障驱动”的被动运维转化为“健康管理”的主动模式。其成功依赖于数据、算法与工程的深度融合:企业需建立从数据采集到模型迭代的全生命周期管理体系,同时兼顾安全性、实时性与成本效益。未来,随着量子计算与神经符号AI的发展,预测维护有望突破现有精度极限,实现设备寿命的“按需设计”,为工业4.0注入更强大的生命力。