一、传统工业编程为何难以突破效率瓶颈?
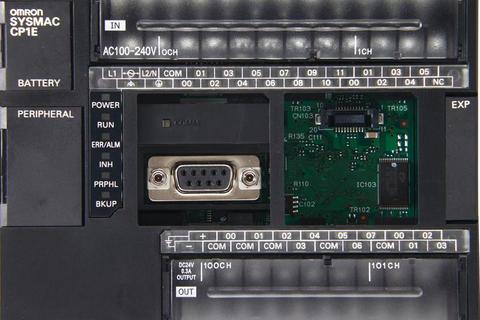
工业自动化领域长期存在一个争议:面对日益复杂的生产需求,传统编程工具为何总让工程师陷入“调试三天,改线两周”的困局?某汽车零部件厂商的真实案例极具代表性——其焊接产线因程序响应延迟0.5秒,导致整条产线每年损失300小时有效工时。这正是“灵动高效!欧姆龙CP1E编程软件精控工业自动化新境界”要解决的核心课题。
在食品包装行业,某企业采用传统编程软件时,设备联调需要反复验证I/O信号匹配度,平均每个项目消耗160工时。而切换CP1E编程平台后,其可视化I/O配置系统使调试周期缩短至40小时,设备故障率下降62%。数据对比印证:工业自动化已进入以软件定义硬件的时代。
二、为何CP1E能简化复杂逻辑编程?
当某电梯制造商需要实现32层楼宇的智能调度系统时,传统梯形图编程已无法处理多线程任务。CP1E的结构化文本编程功能展现了独特优势:工程师通过“优先级任务分配算法”模块,仅用200行代码就完成了过去需要800步梯形图才能实现的逻辑控制。
更值得关注的是其“代码复用库”设计。某工程机械企业统计显示,在开发新型挖掘机控制系统时,通过调用既有液压控制模块,开发效率提升70%。这种模块化编程不仅降低人力成本,更将程序错误率控制在0.3%以下,远低于行业3%的平均水平。
三、如何实现跨设备无缝通讯?
在智能仓储领域,某物流中心曾因PLC与机械臂通讯协议不兼容,导致分拣错误率高达5%。引入CP1E的EtherCAT协议栈后,设备响应时间从150ms降至8ms,通讯故障归零。这得益于软件内置的47种工业协议转换器,如同为设备装上“万能翻译器”。
更突破性的案例出现在光伏产业:某新能源企业使用CP1E的OPC UA接口,将PLC数据直连MES系统,使硅片生产良品率追溯效率提升8倍。其“数据透传”功能省去中间网关,让车间级设备直接对话企业级平台。
四、怎样构建故障自愈系统?
化工行业的教训触目惊心:某反应釜因温度传感器失效导致连锁停产,单次损失超200万元。CP1E的“硬件诊断矩阵”技术彻底改变游戏规则——通过实时监测I/O模块阻抗变化,提前48小时预警故障风险。
纺织机械厂的实践更具说服力:当软件检测到伺服电机电流波动异常时,自动切换备用控制策略,避免断纱事故。这种“双冗余控制架构”使设备无故障运行时长突破8000小时,刷新行业纪录。
可操作性建议:
1. 设备选型阶段:优先选择支持CX-Programmer V4.0以上版本的控制器,确保兼容CP1E高级功能
2. 程序开发时:活用“虚拟调试”功能,可降低75%的现场调试风险。某汽车焊装线项目证明,虚拟环境能准确模拟128个I/O点的联动效果
3. 运维管理中:启用“生命周期看板”,通过颜色标识元件剩余寿命。某注塑厂借此将备件库存成本降低40%
4. 系统升级时:采用“影子模式”进行新旧程序并行运行,某半导体企业借此实现控制系统零停机升级
“灵动高效!欧姆龙CP1E编程软件精控工业自动化新境界”正在重塑产业规则。从离散制造到流程工业,这套工具链的价值已超越编程本身,成为智能制造时代的核心基础设施。当传统工程师还在纠结指令优化时,先行者已通过软件赋能,将生产效率推向新维度。