钣金制造的“智”变:传统工艺如何突破效率与精度的天花板?
在制造业迈向智能化的浪潮中,一个争议性问题始终萦绕在行业心头:当传统钣金制造面临效率低、成本高、精度不足的困境时,究竟是靠“人海战术”延续老路,还是借力软件革新实现破局?
过去十年,中国钣金行业市场规模年均增长超过12%,但人工成本上升和材料浪费问题却让企业利润持续承压。以某车企为例,其钣金件生产中的试模成本一度占总成本的30%,而数字化工具的缺失更导致交货周期长达45天。这样的矛盾,正是“创新智能钣金软件高效赋能精密制造新纪元”的突破口。
一、设计效率翻倍:软件如何“砍掉”80%试错成本?
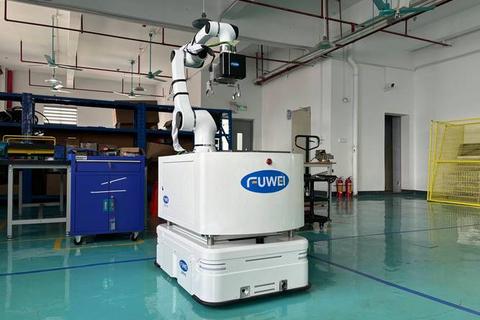
传统钣金设计依赖工程师的经验判断,复杂零件的开发往往需要反复修改模具,耗时耗材。而智能软件的介入,正将这一过程从“经验驱动”转向“数据驱动”。
以大族激光为例,其自主研发的智能设计系统通过集成CAD/CAM技术,将钣金件的展开图生成时间从2小时缩短至10分钟。系统内置的AI算法可自动识别材料特性与加工参数,实时模拟冲压、折弯等工艺的可行性,减少物理试模次数。据其2024年财报显示,该系统帮助客户平均降低试模成本83%,设计周期压缩70%。
另一典型案例是AutoForm汽车钣金仿真软件。该软件通过有限元分析技术,在虚拟环境中预判冲压过程中的开裂、起皱等缺陷。某汽车厂在开发车门内板时,利用该软件优化了17处工艺参数,将模具修改次数从12次减少到2次,节省直接成本超200万元。
二、生产流程重构:智能排产能否让设备“零闲置”?
钣金车间常面临设备利用率低、订单排产混乱的难题。某中小型工厂曾因手动排产导致激光切割机日均闲置4小时,而智能排产系统的引入彻底改变了这一局面。
PGS钣金智能工厂系统的实践颇具代表性。该系统通过APS(高级计划排程)算法,将订单、设备状态、物料库存等数据实时联动。例如,在为奇瑞重工设计的柔性生产线中,系统自动匹配激光切割机与上下料机器人的协作节奏,使设备利用率从65%提升至92%,订单交付准时率提高40%。
更值得关注的是钣金折弯模拟软件的革新。传统折弯工序依赖工人经验判断刀具选择与折弯顺序,而软件可通过3D仿真提前预判干涉问题。某企业引入此类工具后,折弯工序错误率从15%降至1%以下,单件加工时间缩短30%。这些案例印证了“创新智能钣金软件高效赋能精密制造新纪元”的核心价值——让机器更聪明,让生产更流畅。
三、复杂需求破局:小众定制如何实现规模化盈利?
随着新能源汽车、航空航天等领域对异形钣金件的需求激增,企业既要应对“多品种、小批量”的订单特点,又要保证盈利空间。智能软件提供的柔性化解决方案,正在打破规模化与定制化的对立。
DynaForm钣金冲压分析软件在航空领域的应用堪称典范。某飞机零部件制造商需生产曲面弧度误差小于0.1mm的钛合金蒙皮,传统工艺合格率不足50%。通过软件的多物理场耦合仿真,工程师精准预测材料回弹量并自动生成补偿方案,最终将合格率提升至98%,单件成本降低60%。
在消费电子领域,三维扫描检测系统与设计软件的联动更显智能化价值。某手机厂商要求不锈钢中框的118个孔位精度误差≤0.05mm,传统检测需8小时/批次。而搭载AI算法的检测系统可在20分钟内完成全尺寸扫描,并与原始CAD模型自动比对,缺陷识别准确率达99.7%。这种“设计-制造-检测”闭环,正是“创新智能钣金软件高效赋能精密制造新纪元”的终极形态。
破局者的行动指南:三步走策略
对于制造企业而言,拥抱智能化需把握三个关键:
1. 需求导向选工具:中小型企业可优先部署排产优化类软件(如PGS系统),大型企业则需构建从设计到检测的全链条平台。
2. 数据资产重积累:建立工艺参数数据库,例如将不同材料的折弯系数、激光切割速度等数据沉淀为算法优化的燃料。
3. 人机协同再升级:培养既懂钣金工艺又掌握软件操作的复合型人才,例如某车企通过“数字工匠”培训计划,使工程师的仿真分析效率提升3倍。
这场由软件驱动的钣金制造革命,不仅关乎效率与成本,更重新定义了制造业的价值链。当传统车间转型为“数字孪生工厂”,当经验转化为数据资产,“创新智能钣金软件高效赋能精密制造新纪元”的蓝图,正在成为中国企业征战全球市场的底气。