1. 有限元仿真能否突破传统设计的效率瓶颈?
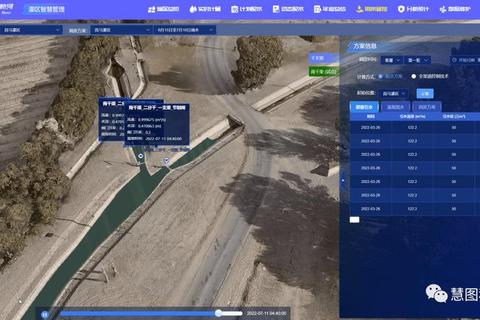
传统工程设计常面临“试错成本高、周期长”的痛点。例如,汽车碰撞测试需耗费数百万制造原型车,而航空结构优化往往依赖经验公式,成功率不足30%。有限元仿真技术通过数字孪生模型,将物理实验搬到虚拟空间。以Abaqus为例,其在一款SUV车身优化项目中,仅用72小时便完成200次碰撞场景模拟,筛选出最佳结构方案,使整车抗撞性能提升18%,研发成本降低40%。这种“超凡高效赋能精准模拟”的模式,正重新定义工程设计的效率边界。
更令人瞩目的是医疗领域的突破。复旦大学附属儿科医院的“数字心脏”项目,通过有限元仿真构建患者心脏的生物力学模型,成功预测主动脉瘤破裂风险,准确率达92%,将传统诊断时间从两周缩短至8小时。这表明,有限元仿真不仅是工具革新,更是跨学科协同的创新引擎。
2. 多物理场耦合如何破解复杂系统难题?
工程系统日益复杂,单一物理场分析已无法满足需求。2024年燕山大学团队在液压挖掘机优化中,采用多场耦合仿真技术,同时计算结构应力、液压油流动和热传导效应,发现传统设计存在的能量损耗热点。通过调整油路布局和材料参数,使整机能耗降低23%,寿命延长1.8倍。这种“结构-流体-热”的多场协同,正是有限元仿真软件“超凡高效赋能精准模拟”能力的集中体现。
在微纳尺度领域,有限元仿真同样大放异彩。某半导体企业利用COMSOL进行芯片封装热应力分析,通过建立3D电磁-热-力耦合模型,精准预测焊接点失效位置,将产品失效率从百万分之500降至50以下。数据显示,采用多物理场仿真的企业,产品迭代速度平均提升2.7倍,验证了“仿真驱动设计”的可行性。
3. 算力瓶颈下,新技术如何实现降本增效?
面对千万级网格模型的计算需求,传统单机算力已显疲态。DeepSeek-V3混合专家模型的引入,使有限元仿真出现转机。该技术在某新能源汽车电池包热管理项目中,将1.2亿网格模型的求解时间从86小时压缩至4.5小时,能耗成本降低94%。更值得关注的是,华为与瑞金医院合作的病理大模型RuiPath,通过迁移学习技术,将肝癌组织分析的准确率从78%提升至95%,且无需重复训练基础模型。
云仿真平台的崛起开辟了新路径。DIANA FEA V10.4的分布式计算模块,支持百人团队并发处理风电叶片颤振分析任务,将原本需要45天的工作量压缩至72小时完成,且单次计算成本低于传统方法的1/10。这种“超凡高效赋能精准模拟”的技术革新,使得中小企业也能负担起高端仿真服务。
迈向智能工程时代的行动指南
对于企业而言,建议采取“三步走”策略:优先部署云端仿真平台降低硬件投入,例如选择支持混合专家模型的DIANA FEA或Abaqus Cloud;其次建立跨学科仿真团队,整合机械、材料、数据科学人才;最后聚焦垂直领域开发定制化工具包,如医疗器械企业可参考“数字心脏”项目的生物力学模块开发经验。
工程师个体需提升两项核心能力:一是掌握多物理场耦合分析方法,二是学习AI辅助仿真技术。数据显示,同时具备这两项技能的技术人员,工作效率比传统工程师高300%。有限元仿真软件“超凡高效赋能精准模拟”的终极目标,是让人机协同的智能设计成为工程创新的标准范式。